1.0
Scope of application and explanation
1.1 Suitable for automotive wiring harness double-wall heat shrinkable tube series products.
1.2 When used in automobile wiring harnesses, at terminal wiring, wire wiring and waterproof end wiring, the specifications and dimensions of the heat shrinkable tube correspond to the reference of the minimum and maximum dimensions of the covered area.
2.0
Use and selection
2.1 Diagram for terminal wiring
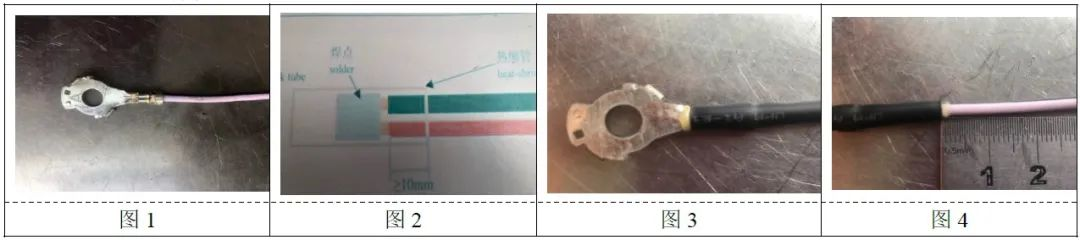
2.2 Diagram for wiring connection
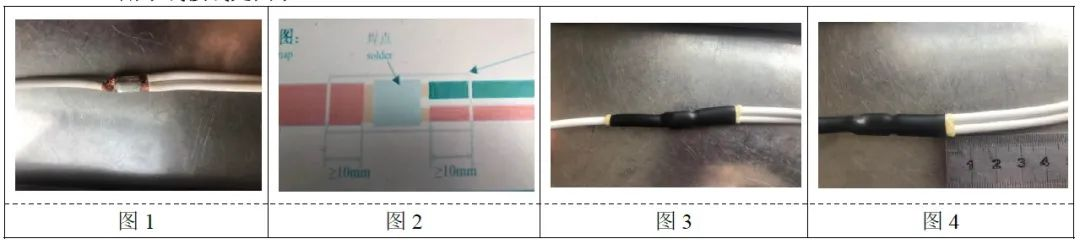
2.3 Instructions for use and selection
2.3.1 According to the minimum and maximum circumference range of the covered part of the terminal (after crimping), the minimum and maximum applicable range of the cable diameter and number of cables, select the appropriate size of the heat shrink tube, see below for details Table 1.
2.3.2 Note that due to different usage environments and methods, the recommended correspondence relationships and ranges in Table 1 are for reference only; it is necessary to determine the appropriate correspondence based on actual use and verification, and form a database accumulation.
2.3.3 In the corresponding relationship in Table 1, the "Application Wire Diameter Example" gives the minimum or maximum wire diameter that can be applied when there are multiple wires of the same wire diameter. However, in actual application, there are multiple wires with different wire diameters at one end of the wire harness contact. At this time, you can compare the "sum of wire diameters" column in Table 1. The actual sum of wire diameters should be within the range of the sum of the minimum and maximum wire diameters, and then verify whether it is applicable.
2.3.4 For terminal wiring or wire wiring, the applicable circumference or wire diameter range of the corresponding heat shrinkable tube needs to be considered, and it should be able to simultaneously cover the minimum and maximum dimensions (circumference or wire diameter) of the covered object. Otherwise, priority should be given to trying to use heat shrinkable tubes of other specifications to see if it can meet the usage requirements; secondly, design and change the wiring method so that it can meet the requirements at the same time; thirdly, add film or rubber particles to the end that cannot meet the maximum value, the minimum Add heat shrink tubing to one end; finally, customize a suitable heat shrink tubing product or other water leakage sealing solution.
2.3.5 The length of the heat shrinkable tube should be determined according to the actual application protection length. Depending on the wire diameter, the heat shrink tube usually used for terminal wiring is 25mm~50mm long, and the heat shrinkable tube used for wire wiring is 40~70mm long. It is recommended that the length of the heat shrinkable tube protective cable insulation is 10mm~30mm, and is selected according to different specifications and sizes. See Table 1 below for details. The longer the protection length, the better the waterproof sealing effect.
2.3.6 Usually, before crimping the terminals or crimping/welding the wires, put the heat shrink tube on the wires first, except for the waterproof end wiring method (that is, all the wires are at one end, and there is no outlet or terminal at the other end) Wiring). After crimping, use a heat shrink machine, hot air gun, or other specific heating method to perform heating shrinkage to shrink the heat shrink tube and fix it in the designed protective position.
2.3.7 After heat shrinking, according to the design or operation requirements, visual inspection is preferred to confirm whether the work quality is good. For example, check the overall appearance for abnormalities such as bulges, uneven appearance (possibly not heat-shrunk), asymmetric protection (the position has moved), surface damage, etc. Pay attention to the propping and puncture caused by jumpers; check both ends Whether the covering is tight, whether the glue overflow and sealing at the wire end are good (usually overflow is 2~5mm); whether the sealing protection at the terminal is good, and whether the glue overflow exceeds the limit required by the design, otherwise it may affect the assembly. etc.
2.3.8 When necessary or required, sampling is required for waterproof seal inspection (special inspection device).
2.3.9 Special reminder: Metal terminals conduct heat quickly when heated. Compared with insulated wires, they absorb more heat (the same conditions and time absorb more heat), conduct heat quickly (heat loss), and consume a lot of heat during heating and shrinkage operations. The heat is theoretically relatively large.
2.3.10 For applications with large wire diameters or a large number of cables, when the hot melt adhesive of the heat shrink tube itself is not enough to fill the gaps between the cables, it is recommended to install rubber particles (ring-shaped) or film (sheet-shaped) To increase the amount of glue between the wires to ensure the waterproof sealing effect. It is recommended that the size of the heat shrink tube is ≥14, the wire diameter is large and the number of cables is large (≥2), as shown in Figures 9, 10, and 11. For example, 18.3 specification heat shrinkable tube, 8.0mm wire diameter, 2 wires, need to add film or rubber particles; 5.0mm wire diameter, 3 wires, need to add film or rubber particles.
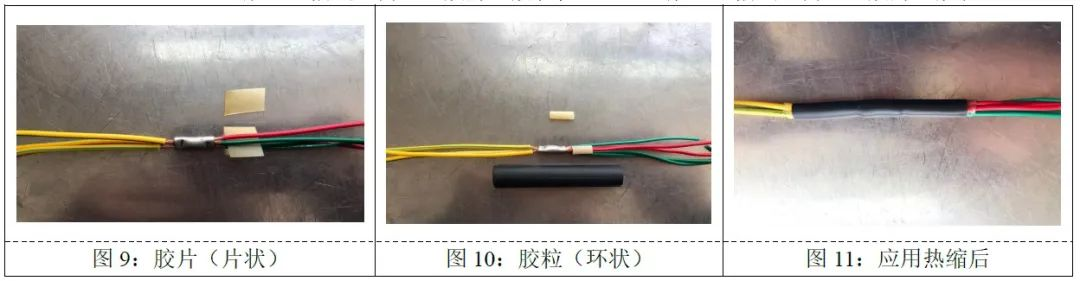
2.4 Selection table of terminal and wire diameter sizes corresponding to heat shrink tube specifications (unit: mm)
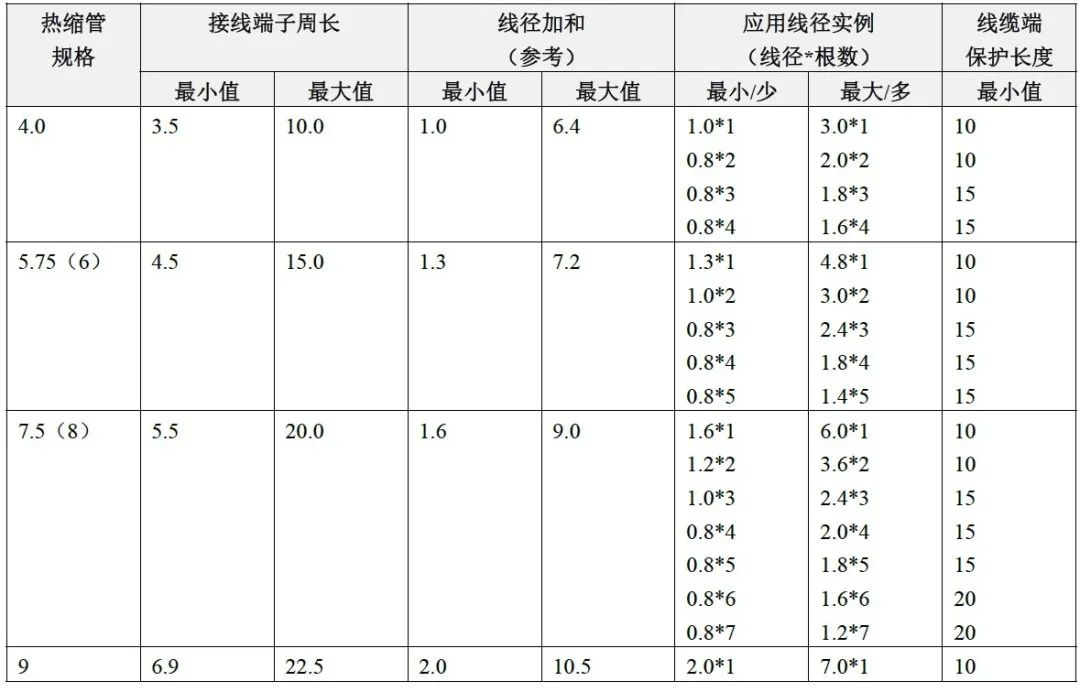
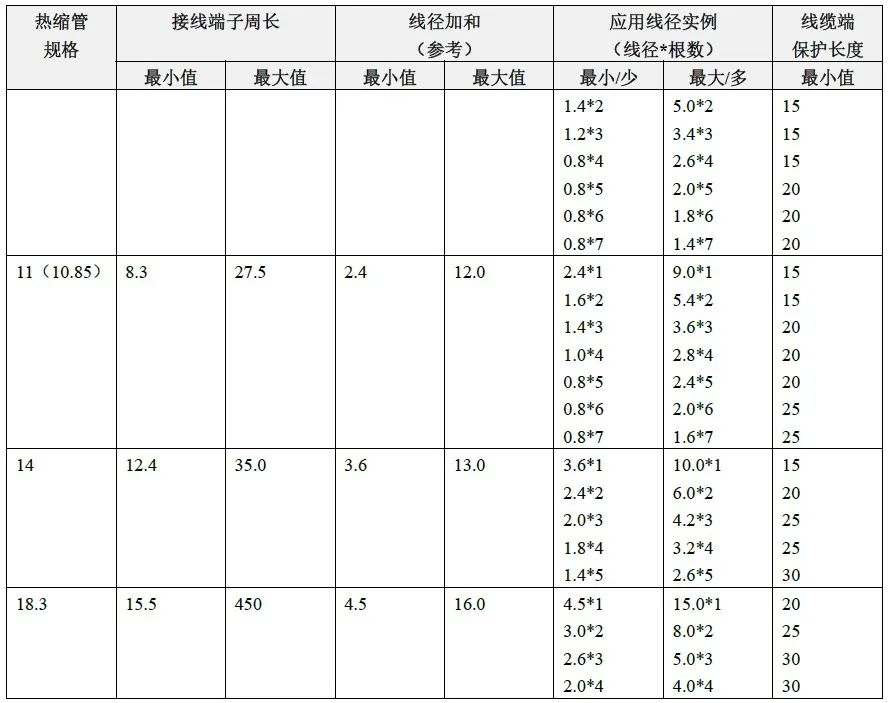
3.0
Heat shrink and heat shrink machine for heat shrink tubing for automotive wiring harnesses
3.1 Crawler type continuous operation heat shrink machine
Common ones include TE (Tyco Electronics)'s M16B, M17, and M19 series heat shrink machines, Shanghai Rugang Automation's TH801, TH802 series heat shrink machines, and Henan Tianhai's self-made heat shrink machines, as shown in Figures 12 and 13.
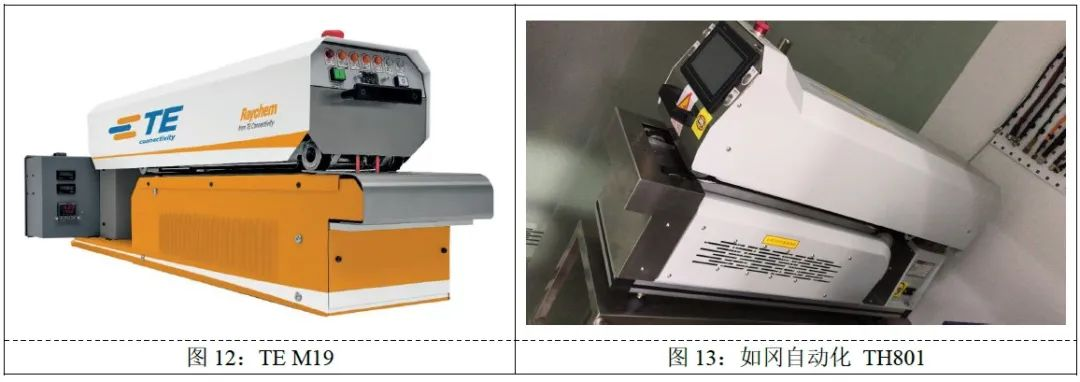
3.2 Through-put heat shrink machine
Common ones include TE (Tyco Electronics)'s RBK-ILS Processor MKIII heat shrink machine, Shanghai Rugang Automation's TH8001-plus digital networked terminal wire heat shrink machine, TH80-OLE series online heat shrink machine, etc., as shown in Figure 14, 15 and 16 shown.
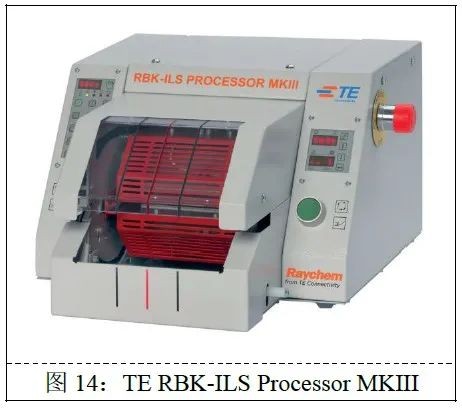
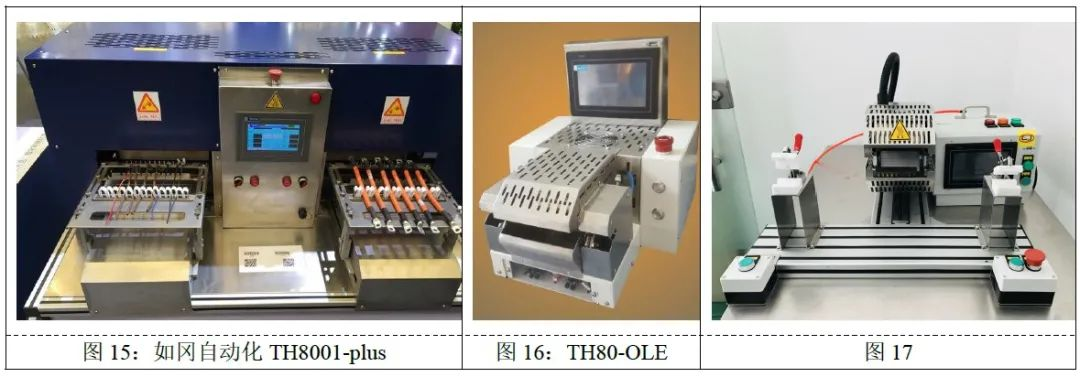
3.3 Instructions for heat shrinking operations
3.3.1 The above types of heat shrink machines are all heat shrink equipment that output a certain amount of heat to the assembly workpiece to be heat-shrunk. After the heat shrink tube on the assembly reaches a sufficient temperature rise, the heat shrink tube shrinks and the hot melt adhesive melts. It plays the role of tightly wrapping, sealing and releasing water.
3.3.2 To be more specific, the heat shrink process is actually the heat shrink tube on the assembly. Under the heating conditions of the heat shrink machine, the heat shrink tube reaches the heat shrink temperature, the heat shrink tube shrinks, and the hot melt adhesive reaches the melt flow temperature. , the hot melt glue flows to fill the gaps and adheres to the covered workpiece, thereby making a quality waterproof seal or insulating protective assembly component.
3.3.3 Different forms of heat shrink machines have different heating capabilities, that is, the amount of heat output to the assembly workpiece per unit time, or heat output efficiency, is different. Some are faster, some are slower, the heat shrinking operation time will be different (the crawler machine adjusts the heating time by speed), and the equipment temperature that needs to be set will be different.
3.3.4 Even heat shrink machines of the same model will have different heat output efficiencies due to differences in the heating workpiece output value of the equipment, the age of the equipment, etc.
3.3.5 The set temperatures of the above heat shrink machines are generally between 500°C and 600°C, coupled with appropriate heating time (the crawler machine adjusts the heating time through speed) to perform heat shrinkage operations.
3.3.6 However, the set temperature of the heat shrink equipment does not represent the actual temperature reached by the heat shrink assembly after being heated. In other words, the heat shrink tube and its assembly workpieces do not need to reach the several hundred degrees set by the heat shrink machine. Generally, they need to reach a temperature rise of 90°C to 150°C before they can be heat shrunk and function as a water release seal.
3.3.7 Appropriate process conditions should be selected for heat shrinking operations based on the size of the heat shrink tube, the hardness and softness of the material, the volume and heat absorption characteristics of the covered object, the volume and heat absorption characteristics of the tooling fixture, and the ambient temperature.
3.3.8 You can usually use a thermometer and put it into the cavity or tunnel of the heat shrink equipment under process conditions, and observe the maximum temperature that the thermometer reaches in real time as a calibration of the heat output capability of the heat shrink equipment at that time. (Note that under the same heat shrinking process conditions, the heating temperature rise of the thermometer will be different from the heating temperature rise of the heat shrink assembly workpiece due to the difference in volume and temperature rise efficiency after heating, so the temperature rise of the thermometer The measured temperature rise is only used as a reference calibration for process conditions and does not represent the temperature rise that the heat shrink assembly will reach)
3.3.9 The pictures of the thermometer are shown in Figures 18 and 19. Generally, a specific temperature probe is required.
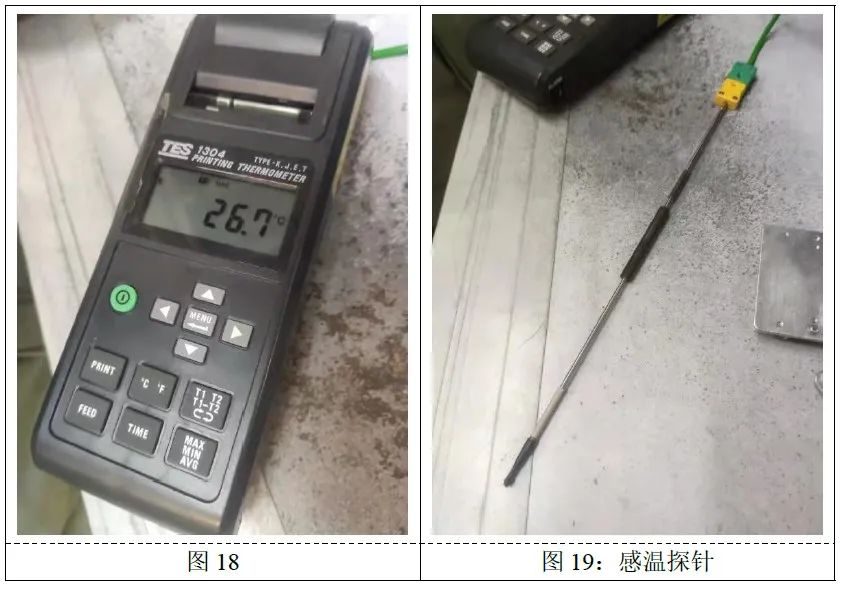
Post time: Nov-14-2023