As aluminum conductors are increasingly used in automotive wiring harnesses, this article analyzes and organizes the connection technology of aluminum power wiring harnesses, and analyzes and compares the performance of different connection methods to facilitate the later selection of aluminum power wiring harness connection methods.
01 Overview
With the promotion of the application of aluminum conductors in automobile wiring harnesses, the use of aluminum conductors instead of traditional copper conductors is gradually increasing. However, in the application process of aluminum wires replacing copper wires, electrochemical corrosion, high temperature creep, and conductor oxidation are problems that must be faced and solved during the application process. At the same time, the application of aluminum wires replacing copper wires must meet the requirements of the original copper wires. Electrical and mechanical properties to avoid performance degradation.
In order to solve problems such as electrochemical corrosion, high temperature creep, and conductor oxidation during the application of aluminum wires, there are currently four mainstream connection methods in the industry, namely: friction welding and pressure welding, friction welding, ultrasonic welding, and plasma welding.
The following is an analysis and performance comparison of the connection principles and structures of these four types of connections.
02 Friction welding and pressure welding
Friction welding and pressure joining, first use copper rods and aluminum rods for friction welding, and then stamp the copper rods to form electrical connections. The aluminum rods are machined and shaped to form aluminum crimp ends, and copper and aluminum terminals are produced. Then the aluminum wire is inserted into the aluminum crimping end of the copper-aluminum terminal and hydraulically crimped through traditional wire harness crimping equipment to complete the connection between the aluminum conductor and the copper-aluminum terminal, as shown in Figure 1.
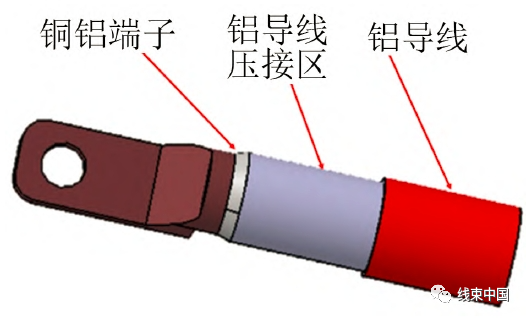
Compared with other connection forms, friction welding and pressure welding form a copper-aluminum alloy transition zone through friction welding of copper rods and aluminum rods. The welding surface is more uniform and dense, effectively avoiding the thermal creep problem caused by different thermal expansion coefficients of copper and aluminum. , In addition, the formation of the alloy transition zone also effectively avoids electrochemical corrosion caused by the different metal activities between copper and aluminum. Subsequent sealing with heat shrink tubes is used to isolate salt spray and water vapor, which also effectively avoids the occurrence of electrochemical corrosion. Through the hydraulic crimping of the aluminum wire and the aluminum crimp end of the copper-aluminum terminal, the monofilament structure of the aluminum conductor and the oxide layer on the inner wall of the aluminum crimp end are destroyed and peeled off, and then the cold is completed between the single wires and between the aluminum conductor conductor and the inner wall of the crimp end. The welding combination improves the electrical performance of the connection and provides the most reliable mechanical performance.
03 Friction welding
Friction welding uses an aluminum tube to crimp and shape the aluminum conductor. After cutting off the end face, friction welding is performed with the copper terminal. The welding connection between the wire conductor and the copper terminal is completed through friction welding, as shown in Figure 2.
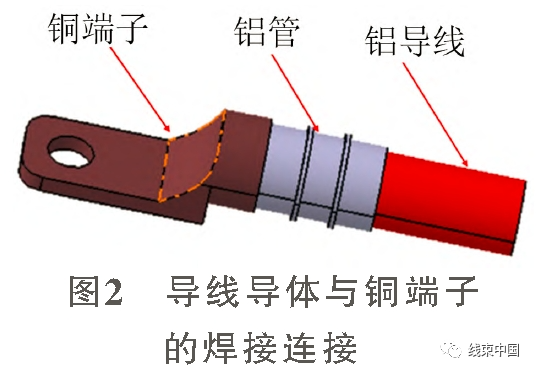
Friction welding connects aluminum wires. First, the aluminum tube is installed on the conductor of the aluminum wire through crimping. The monofilament structure of the conductor is plasticized through crimping to form a tight circular cross-section. Then the welding cross-section is flattened by turning to complete the process. Preparation of welding surfaces. One end of the copper terminal is the electrical connection structure, and the other end is the welding connection surface of the copper terminal. The welding connection surface of the copper terminal and the welding surface of the aluminum wire are welded and connected through friction welding, and then the welding flash is cut and shaped to complete the connection process of the friction welding aluminum wire.
Compared with other connection forms, friction welding forms a transition connection between copper and aluminum through friction welding between copper terminals and aluminum wires, effectively reducing electrochemical corrosion of copper and aluminum. The copper-aluminum friction welding transition zone is sealed with adhesive heat shrink tubing in the later stage. The welding area will not be exposed to air and moisture, further reducing corrosion. In addition, the welding area is where the aluminum wire conductor is directly connected to the copper terminal through welding, which effectively increases the pull-out force of the joint and makes the processing process simple.
However, the disadvantages also exist in the connection between aluminum wires and copper-aluminum terminals in Figure 1. The application of friction welding to wire harness manufacturers requires separate special friction welding equipment, which has poor versatility and increases the investment in fixed assets of wire harness manufacturers. Secondly, in friction welding During the process, the monofilament structure of the wire is directly friction welded with the copper terminal, resulting in cavities in the friction welding connection area. The presence of dust and other impurities will affect the final welding quality, causing instability in the mechanical and electrical properties of the welding connection.
04 Ultrasonic welding
Ultrasonic welding of aluminum wires uses ultrasonic welding equipment to connect aluminum wires and copper terminals. Through the high-frequency oscillation of the welding head of the ultrasonic welding equipment, the aluminum wire monofilaments and the aluminum wires and copper terminals are connected together to complete the aluminum wire and The connection of copper terminals is shown in Figure 3.
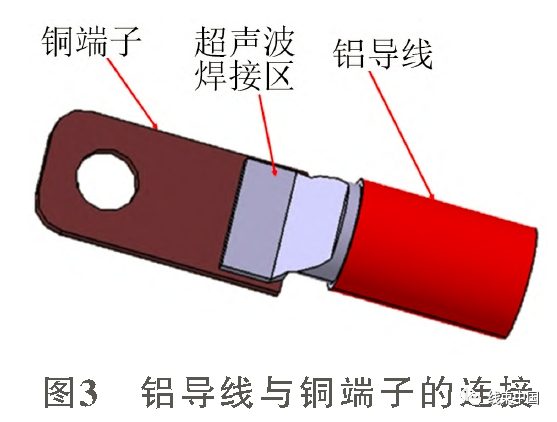
Ultrasonic welding connection is when aluminum wires and copper terminals vibrate at high-frequency ultrasonic waves. Vibration and friction between copper and aluminum complete the connection between copper and aluminum. Because both copper and aluminum have a face-centered cubic metal crystal structure, in a high-frequency oscillation environment Under this condition, the atomic replacement in the metal crystal structure is completed to form an alloy transition layer, effectively avoiding the occurrence of electrochemical corrosion. At the same time, during the ultrasonic welding process, the oxide layer on the surface of the aluminum conductor monofilament is peeled off, and then the welding connection between the monofilaments is completed, which improves the electrical and mechanical properties of the connection.
Compared with other connection forms, ultrasonic welding equipment is a commonly used processing equipment for wire harness manufacturers. It does not require new fixed asset investment. At the same time, the terminals use copper stamped terminals, and the terminal cost is lower, so it has the best cost advantage. However, disadvantages also exist. Compared with other connection forms, ultrasonic welding has weaker mechanical properties and poor vibration resistance. Therefore, the use of ultrasonic welding connections is not recommended in high-frequency vibration areas.
05 Plasma welding
Plasma welding uses copper terminals and aluminum wires for crimp connection, and then by adding solder, the plasma arc is used to irradiate and heat the area to be welded, melt the solder, fill the welding area, and complete the aluminum wire connection, as shown in Figure 4.
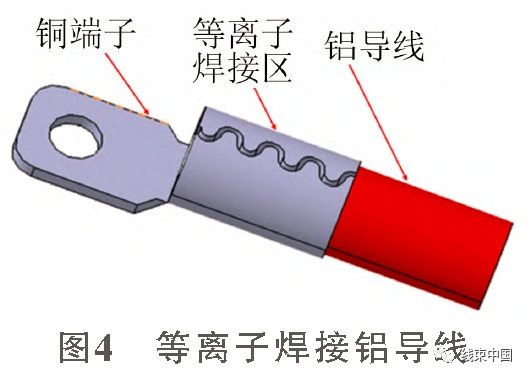
Plasma welding of aluminum conductors first uses plasma welding of copper terminals, and the crimping and fastening of the aluminum conductors is completed by crimping. The plasma welding terminals form a barrel-shaped structure after crimping, and then the terminal welding area is filled with zinc-containing solder, and the crimped end is Add zinc-containing solder. Under the irradiation of plasma arc, the zinc-containing solder is heated and melted, and then enters the wire gap in the crimping area through capillary action to complete the connection process of copper terminals and aluminum wires.
Plasma welding aluminum wires complete the fast connection between the aluminum wires and the copper terminals through crimping, providing reliable mechanical properties. At the same time, during the crimping process, through a compression ratio of 70% to 80%, the destruction and peeling off of the oxide layer of the conductor is completed, effectively Improve electrical performance, reduce contact resistance of connection points, and prevent heating of connection points. Then add zinc-containing solder to the end of the crimping area, and use a plasma beam to irradiate and heat the welding area. The zinc-containing solder is heated and melted, and the solder fills the gap in the crimping area through capillary action, achieving salt spray water in the crimping area. Vapor isolation avoids the occurrence of electrochemical corrosion. At the same time, because the solder is isolated and buffered, a transition zone is formed, which effectively avoids the occurrence of thermal creep and reduces the risk of increased connection resistance under hot and cold shocks. Through plasma welding of the connection area, the electrical performance of the connection area is effectively improved, and the mechanical properties of the connection area are also further improved.
Compared with other connection forms, plasma welding isolates copper terminals and aluminum conductors through the transition welding layer and strengthened welding layer, effectively reducing the electrochemical corrosion of copper and aluminum. And the reinforced welding layer wraps the end face of the aluminum conductor so that the copper terminals and the conductor core will not come into contact with air and moisture, further reducing corrosion. In addition, the transition welding layer and the reinforced welding layer tightly fix the copper terminals and aluminum wire joints, effectively increasing the pull-out force of the joints and making the processing process simple. However, disadvantages also exist. The application of plasma welding to wire harness manufacturers requires separate dedicated plasma welding equipment, which has poor versatility and increases the investment in fixed assets of wire harness manufacturers. Secondly, in the plasma welding process, the solder is completed by capillary action. The gap filling process in the crimping area is uncontrollable, resulting in unstable final welding quality in the plasma welding connection area, resulting in large deviations in electrical and mechanical performance.
Post time: Feb-19-2024